The basic principle of the indirect method with Scintillator is to take a layer of a material that converts X-ray quants to light quants and put it onto a photo-diode structure to measure the light input. The "classical" photo-diode arrays are made of
and this material has proven a good X-ray hardness even for hard NDT applications. The amorphous silicon layer is quite thin (a few µm thick film) and it is deposited onto a hard substrate*, such as glass, to guarantee a very flat surface and stability.
The scintillator is a foil with a material that converts X-ray quants to light quants. During "flying through" this scintillation layer the X-ray quants are slowed down a little bit and this energy is converted to light. As thicker the scintillation layer is as more light quants can be produced. Finally the X-ray quant passes the layer and hits the semiconductor plate below the scintillation layer - now with lower energy as before when touching the scintillation layer. Within a thick scintillation screen one X-ray quant could produce more than thousands of light quants.
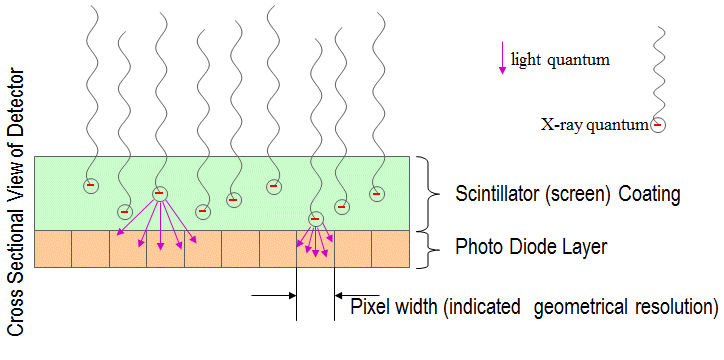
The light quants which are produced can fly in any direction. To increase the efficiency sometimes the upper surface of the scintillator is coated with a reflection layer to reflect the light quants and increase the efficiency by a best case factor of 2. But it is obvious that the light quants not only hit the photo diode just below the place of conversion (what is the best case) - it could also hit the pixel more far away and creates an unsharpness.
Therefore the thickness of the scintillation layer should fit to the pixel size. Here is the reason that detector with large pixel have higher efficiency compared to a detector with smaller pixel - if the scintillator fits to the pixel size. As there are sometimes detectors with small pixel but thick scintillators a user should look at the spatial resolution (SR
b) instead of the pixel size when selecting or comparing a DDA for his application.
*Hint: In 2015 first attempt were done to put the amorphous silicon film onto a flexible substrate like plastic for a flexible detector. With this flexibility the detector could also be bent around a pipe for weld inspection - which is today the application for film or CR due to this unique feature.